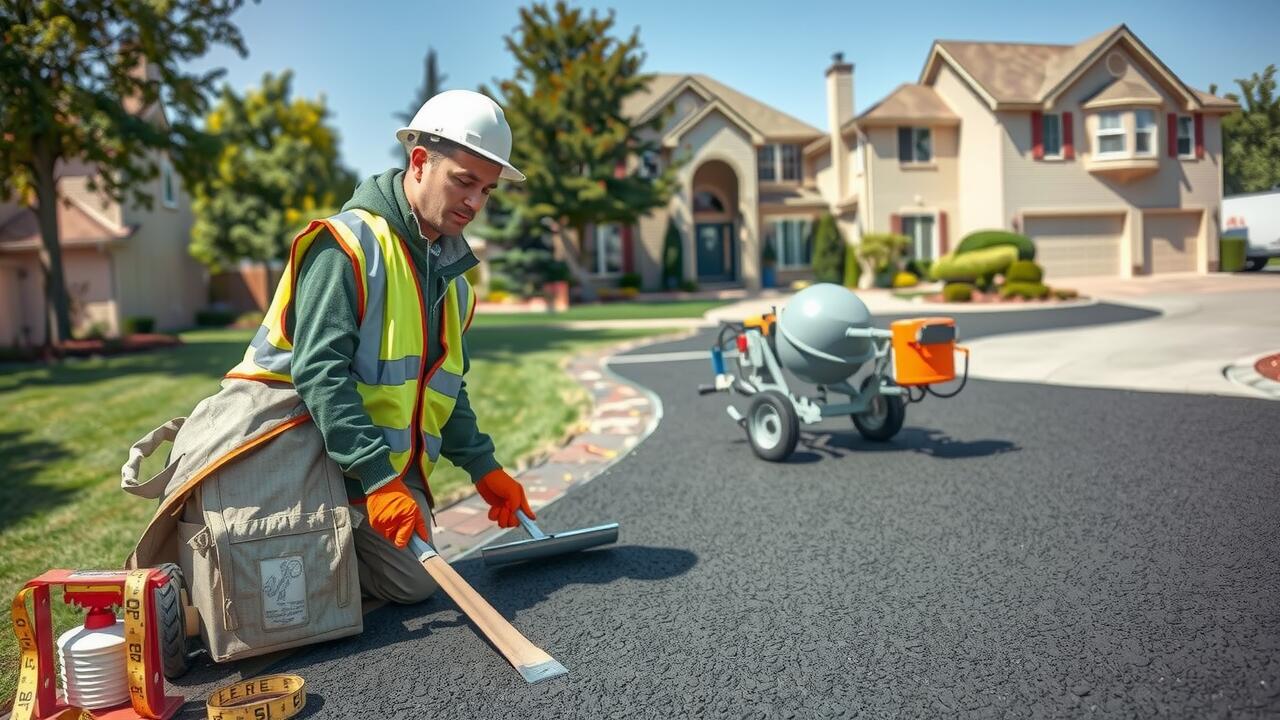
Table Of Contents
Maintenance and Longevity Factors
Regular maintenance plays a crucial role in extending the lifespan of a newly installed driveway. Different materials require different care routines. For instance, a concrete driveway needs periodic sealing to prevent cracking, while asphalt may require a sealant to protect it from the elements. Regular cleaning can help remove dirt and debris that contribute to deterioration. Homeowners in Plymouth, Minnesota can expect that performing these basic maintenance tasks will enhance the durability of their driveway.
The longevity of a driveway also relates to the quality of materials chosen for installation. Higher-quality options typically result in lower long-term costs due to their resilience against wear and tear. For example, a well-installed paver driveway may last significantly longer than asphalt. Homeowners must consider factors such as climate and expected traffic when evaluating materials for Plymouth, Minnesota driveway installation. Making an informed choice about both the material and maintenance will lead to a driveway that serves its purpose for many years.
Future Expenses to Keep in Mind
When planning for driveway installation, it is essential to consider future expenses that may arise after the initial phase. Regular maintenance plays a crucial role in the longevity of the driveway. For instance, sealing asphalt surfaces every few years protects against cracking caused by weather elements. Concrete driveways also require certain upkeep, such as cleaning and sealant application to prevent stains and surface deterioration. Homeowners should factor these potential costs into their overall budget.
In addition to regular maintenance, it is wise to anticipate costs related to repairs and enhancements. Over time, wear and tear could lead to the need for patching or resurfacing. If a homeowner decides to modify the layout or expand the driveway, additional expenses will incur. With projects like Minnesota driveway installation, inflation and fluctuating material prices may also influence future budgeting decisions, making it crucial to keep these factors in mind.
Cost Variations by Driveway Type
The type of driveway material chosen will significantly influence the overall cost of installation. Concrete driveways typically have a moderate price range, often providing a durable surface with a lifespan that can extend beyond 30 years with proper care. Asphalt driveways tend to be less expensive upfront, but maintenance costs may accumulate over time, particularly in extreme weather conditions. Pavers, while aesthetically appealing and customizable, usually represent the higher end of the cost spectrum due to their intricate installation process.
When evaluating the costs associated with Minnesota Driveway Installation, it becomes clear that regional variations can also play a critical role. Labor costs, material availability, and even local regulations can impact the final price. Homeowners in Minnesota may notice that the harsh winter climate requires specific materials and installation techniques, which could increase initial expenses. Carefully considering each type of driveway in the context of local factors will provide a clearer estimate of the total investment needed.
Comparing Concrete, Asphalt, and Pavers
Concrete, asphalt, and pavers represent three popular choices for driveway installations, each providing distinct benefits and drawbacks. Concrete offers a sleek, modern appearance and high durability, making it a go-to option for many homeowners. While its initial installation cost can be higher than asphalt, concrete typically requires less frequent repair and maintenance. In contrast, asphalt is often praised for its affordability and quicker installation process, but it can necessitate more maintenance over time, such as sealcoating and crack repairs. Homeowners in Saint Michael, Minnesota, should weigh these factors to decide which material best suits their needs.
Pavers, crafted from durable materials like brick or stone, can create a unique and visually appealing driveway. This choice allows for customization in design, making it suitable for those looking to enhance curb appeal. However, the cost of pavers tends to be higher than both concrete and asphalt, in addition to potentially requiring more labor during installation. Exploring each option's longevity in various weather conditions is crucial, especially in regions like Saint Michael, Minnesota, where freeze-thaw cycles can affect driveway performance over time.
Regional Price Differences
Regional price differences play a significant role in the overall cost of driveway installation. Local demand for services, availability of materials, and labor costs can all fluctuate, leading to variations in pricing. For instance, urban areas might experience higher expenses due to a greater demand for skilled labor and specialized equipment. Conversely, rural locations may offer lower prices, but this can depend on the proximity to suppliers and installers.
In Plymouth, Minnesota, driveway installation prices may be affected by local regulations and weather conditions. Harsh winters could necessitate different materials or methods compared to warmer regions, influencing the total cost. Additionally, seasonal demand patterns can lead to price adjustments, with spring and summer typically seeing increased activity and potentially higher fees for installation services. Understanding these factors can help homeowners in Plymouth better prepare for their driveway projects.
How Location Affects Installation Costs
Location plays a crucial role in determining the expenses associated with driveway installation. Factors such as local labor costs, regional material availability, and specific building codes can significantly influence the overall price. A driveway installation in an urban area may have different rates compared to a rural location due to varying demand and competition among contractors.
In Saint Michael, Minnesota, driveway installation costs may reflect regional trends and community preferences. The climate can also affect the choice of materials, with frost-resistant options being more common in colder regions. Homeowners should consider these variables when budgeting for their project to ensure a more accurate estimation of total expenses.
FAQS
What are the main factors that affect driveway installation costs?
The main factors include the type of materials used, service fees for labor, regional price variations, and any additional features such as drainage systems or decorative elements.
How can I estimate the cost of materials for my driveway?
To estimate material costs, measure the area of your driveway and research local prices for your chosen material, such as concrete, asphalt, or pavers. Don’t forget to include a contingency for waste and overage.
Are there any additional costs associated with driveway installation?
Yes, additional costs can include site preparation, grading, permits, and maintenance tools. It's important to factor in these potential expenses to get an accurate total.
How do labor costs vary by location?
Labor costs can vary significantly by region due to differences in living expenses, demand for installation services, and local labor rates. It's advisable to get multiple quotes from local contractors.
What is the average lifespan of different driveway materials, and how does that affect long-term costs?
Concrete driveways typically last 25-30 years, asphalt lasts about 15-20 years, while pavers can last up to 50 years with proper maintenance. Choosing a material with a longer lifespan may reduce long-term costs related to replacement and repairs.