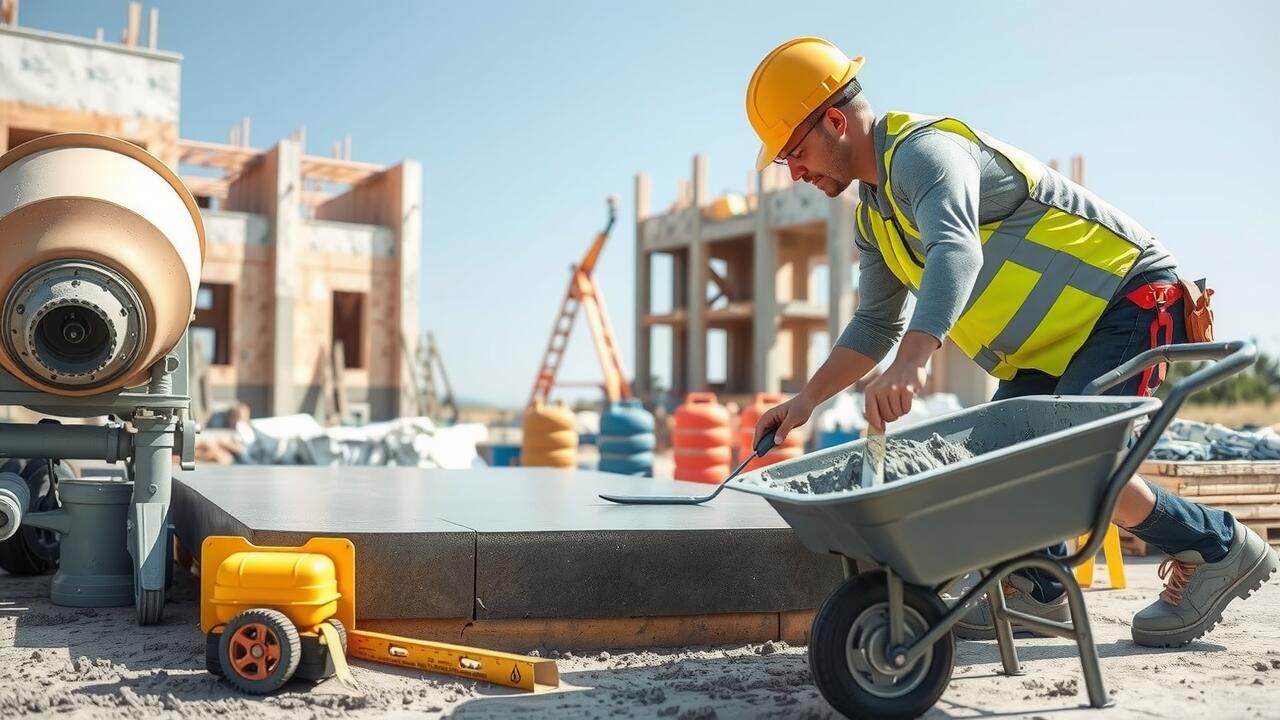
Table Of Contents
Permits and Regulations
When planning a concrete slab installation, it's essential to consider the necessary permits and regulations specific to your location. Authorities often require permits to ensure that construction meets safety and zoning standards. For residents engaging in Saint Michael, Minnesota concrete slab installation, checking with local building departments can provide guidance on the required documentation and inspections.
The importance of compliance with local regulations cannot be overstated. Not only does obtaining the correct permits help avoid potential fines, but it also ensures that the project adheres to community guidelines. Engaging with professionals familiar with the permitting process can streamline this part of the project and prevent delays in construction.
Checking Local Building Codes
Before beginning any construction project, it is essential to check local building codes. These regulations dictate various aspects of construction, including permissible materials, thickness requirements, and design specifications for concrete slabs. Noncompliance can result in fines or the need for costly modifications, so understanding these codes is crucial for a successful installation project.
For residents in Rogers, Minnesota considering a concrete slab installation, it's advisable to consult the local building department. They can provide detailed information on any necessary permits and the specific regulations that apply to residential or commercial applications. This ensures that the project adheres to safety standards and local guidelines, ultimately facilitating a smoother construction process.
Optimal Weather Conditions for Pouring Concrete
Optimal weather conditions play an essential role in the successful pouring of concrete. Ideally, temperatures between 50 and 85 degrees Fahrenheit are recommended for curing concrete effectively. At these temperatures, the chemical reactions within the concrete happen at an optimal rate, ensuring maximum strength and durability. Rogers, Minnesota, typically experiences a wide range of temperatures throughout the year. It’s important to plan the concrete pour during a time when the weather forecast looks favorable to avoid potential complications.
Humidity levels also impact the pouring process. High humidity can slow down the curing of concrete, while low humidity may lead to rapid evaporation, which can hinder setting and lead to a weak surface. It is critical to monitor both temperature and humidity when planning a concrete slab project. For those considering a Rogers, Minnesota concrete slab installation, understanding these weather factors can help in achieving the best results for your project.
How Weather Affects Curing and Setting
Weather conditions play a significant role in the curing and setting process of a concrete slab. Temperature extremes can adversely affect the hydration process of the concrete. High temperatures can lead to rapid evaporation of water from the surface, potentially causing cracks and weakening the slab. Conversely, cold weather can slow down curing, increasing the time needed for the concrete to gain strength. In places like Rogers, Minnesota, concrete slab installation requires careful consideration of seasonal weather patterns to ensure optimal results.
Moisture levels in the air also contribute to the curing environment. High humidity can extend the setting time, while low humidity may increase the risk of surface defects. Rain during curing can wash away essential components or create inconsistencies in the slab. Proper planning around local weather reports can minimize risks associated with these elements. Taking all these factors into account is crucial for successful concrete slab installation, particularly in areas with unpredictable climates.
Estimating Total Project Costs
Estimating the total project costs for installing a 24x24 concrete slab involves a careful breakdown of material and labor expenses. The primary materials needed include concrete, rebar, gravel for the base, and possibly forms or reinforcement mesh. In addition to these materials, one must account for delivery fees and any additional tools required for the job. In regions like Rogers, Minnesota, the local market can influence these costs. It’s prudent to get quotes from multiple suppliers to ensure the best price for concrete and related materials.
Labor costs can vary significantly based on the complexity of the project and the contractors available in your area. Typically, hiring professionals for Rogers, Minnesota concrete slab installation will increase the overall expense, but it may provide a higher-quality finish and reduce the risk of errors. Consider how many hours the job might take and the hourly rate for skilled labor. By summing up both material and labor costs, property owners can obtain a comprehensive estimate of the investment required to pour a concrete slab of this size.
Combining Material and Labor Expenses
Calculating the total investment for a 24x24 concrete slab requires a careful assessment of both material and labor costs. In the case of Rogers, Minnesota concrete slab installation, material expenses typically cover concrete mix, reinforcement materials, formwork, and any additional supplies required for surface finishing. The average price of concrete per cubic yard, along with any additives or tools necessary for the job, contributes significantly to the overall cost.
Labor costs also play a crucial role in the financial estimate, as skilled labor is needed for proper installation. Factors such as the complexity of the job, the experience of the workforce, and local wage rates can influence the total labor expenses. In many projects, investing in experienced contractors ensures a well-executed installation, which can provide long-term value and durability for the slab.
FAQS
What materials are typically needed to pour a 24x24 concrete slab?
The main materials required include concrete mix, gravel for the base, rebar or wire mesh for reinforcement, and potentially vapor barriers or forms.
How do local building codes affect the cost of pouring a concrete slab?
Local building codes may require specific materials, thicknesses, or reinforcement standards, which can influence both the materials and labor costs associated with the project.
What is the average cost of labor for pouring a concrete slab?
Labor costs can vary widely based on location and contractor experience, but typically range from $2 to $4 per square foot of slab.
How does weather impact the process of pouring a concrete slab?
Weather affects the curing and setting times of the concrete; extreme temperatures (hot or cold) can lead to cracking or improper curing, potentially increasing costs if a rescheduling or additional materials are needed.
Are permits necessary for pouring a concrete slab?
Yes, many municipalities require permits for concrete work, especially for projects involving significant quantities of concrete or those that affect drainage and property lines. Always check local regulations before starting.