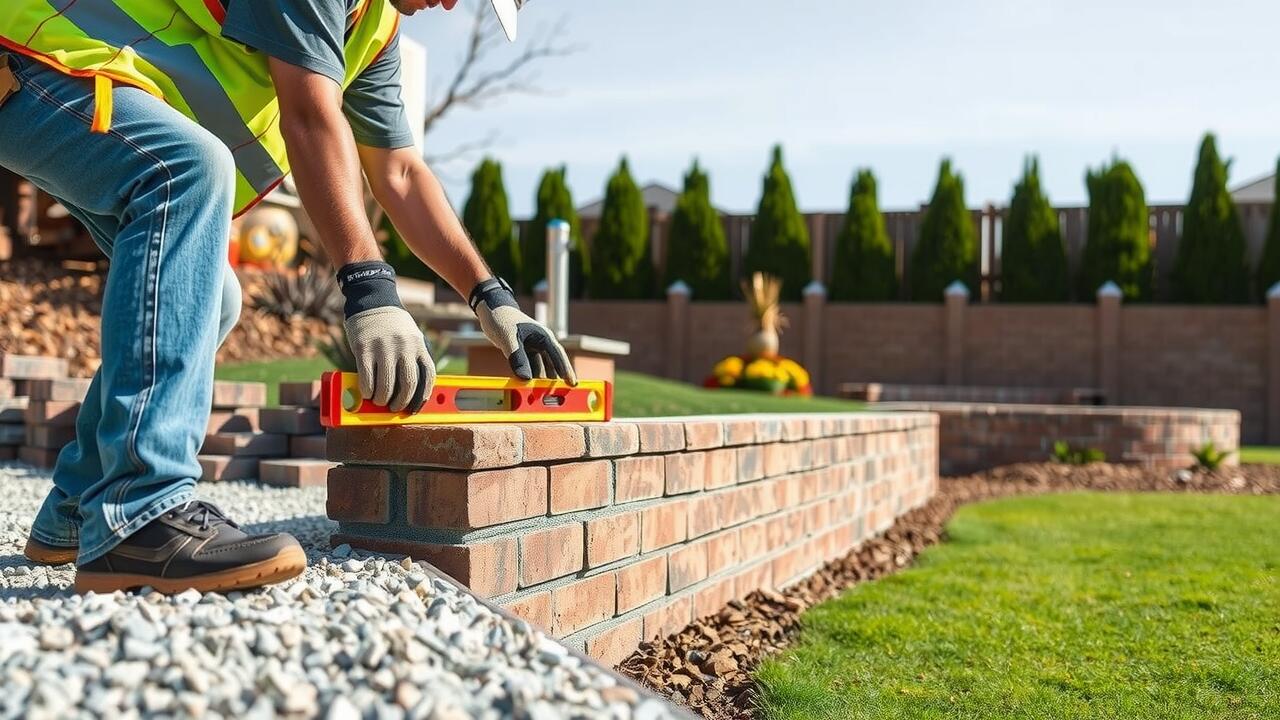
Table Of Contents
Not Using Proper Tools
Using the right tools is crucial for a successful retaining wall installation. Homeowners often underestimate the importance of having precise equipment, which can lead to poor results. For tasks like digging, leveling, and cutting blocks, using the correct tools, such as a shovel, level, and masonry saw, ensures that the wall will be structurally sound.
In Maple Grove, Minnesota retaining wall installation, having the proper tools can make a significant difference in the efficiency of the project. Without the right equipment, the installation may take longer and result in uneven walls. This could create problems down the line, including drainage issues and potential collapse, making it vital to invest in quality tools before starting the project.
Essential Tools for Installation
When undertaking a Minnesota retaining wall installation, having the right tools is crucial for achieving a successful result. A level ensures that each course of blocks is even, which is essential for stability. A rubber mallet helps set the blocks in place without damaging them, while a measuring tape gets tight measurements for proper spacing. Additionally, a shovel and rake are necessary for preparing the site and achieving the proper grade.
Safety gear should not be overlooked. A good pair of work gloves protects hands from rough edges, while safety goggles shield the eyes from debris during cutting or digging. Making sure to have all essential tools on hand helps streamline the installation process. This preparation ultimately contributes to building a durable and aesthetically pleasing retaining wall.
Overlooking Building Codes
Building codes serve as crucial guidelines for any construction project, including retaining walls. Neglecting these regulations can lead to structural failures and legal issues. In areas like Rogers, Minnesota, retaining wall installation often requires permits and adherence to specific codes, which are intended to ensure safety and durability. Familiarizing oneself with local requirements is essential for avoiding future complications.
Compliance with building codes often involves considerations such as wall height, drainage systems, and material specifications. These regulations aim to protect homeowners and their properties from potential hazards. Skipping the step of checking local codes can lead to costly repairs down the line or even penalties from local authorities. Properly following these guidelines in Rogers, Minnesota, not only enhances the integrity of your retaining wall but also promotes peace of mind for the property owner.
Importance of Compliance with Regulations
Adhering to local building codes is crucial when planning a retaining wall installation. Regulations often dictate the height, design, and materials used, ensuring safety and structural integrity. Failing to comply with these codes can lead to costly fines or the need for a complete rebuild. In Maple Grove, Minnesota, retaining wall installation requires understanding specific guidelines that protect property owners and neighboring areas from potential hazards.
Building permits are typically needed before starting your project. This process ensures that the design meets community standards and helps prevent issues related to drainage and soil erosion. By following the regulations set forth by local authorities, homeowners can create a stable and reliable retaining wall that withstands the test of time while also enhancing the landscape.
Failing to Account for Soil Pressure
Ignoring soil pressure can lead to significant problems when building retaining walls. Soil exerts pressure on the wall, especially in areas where drainage systems are inadequate. The type of soil, its moisture content, and the slope of the land all play crucial roles in this dynamic. Proper analysis is essential to determine how much pressure the retaining wall will need to withstand. Failure to account for these factors may result in a wall that is unable to support the weight of the soil, potentially leading to collapse.
In Saint Michael, Minnesota retaining wall installation, it is particularly important to evaluate soil conditions before starting a project. Local soil types and their properties can vary greatly and should be considered in the planning stages. A thorough soil test can provide insight into the necessary adjustments for maintaining wall stability. Taking these precautions not only enhances the wall’s durability but also ensures the safety of the surrounding property.
The Role of Soil in Retaining Wall Stability
Soil plays a critical role in the stability and durability of retaining walls. It is essential to understand the different types of soil and their drainage characteristics. Sandy soil tends to drain well but may not provide enough support, while clay soil can retain water, potentially leading to increased pressure against the wall. Evaluating the soil condition before installation helps determine the necessary precautions to ensure long-term stability.
In Rogers, Minnesota retaining wall installation, factors such as soil type and moisture content should not be overlooked. Proper drainage systems can mitigate pressure buildup behind the wall, preventing potential failure. Furthermore, the overall design of the wall must accommodate soil load and local geological conditions. This attention to soil dynamics will enhance the effectiveness of the retaining structure while ensuring compliance with engineering standards.
FAQS
What are the most common mistakes made when installing retaining wall blocks?
The most common mistakes include not using proper tools, overlooking building codes, failing to account for soil pressure, improper drainage, neglecting to level the base, using low-quality materials, and not considering the wall's height and design.
Why is it important to use proper tools for retaining wall installation?
Using proper tools ensures accuracy and efficiency during the installation process, which helps maintain the structural integrity of the wall and reduces the risk of errors that could lead to failure.
What are the potential consequences of overlooking building codes when installing a retaining wall?
Overlooking building codes can lead to structural instability, legal issues, and potential fines. Additionally, failure to comply with regulations may result in costly repairs or the need to rebuild the wall.
How does soil pressure affect the stability of a retaining wall?
Soil pressure is a crucial factor in retaining wall stability. Failing to account for the weight and type of soil can lead to excessive pressure on the wall, causing it to bulge or collapse over time.
What role does drainage play in retaining wall installation?
Proper drainage is essential to prevent water buildup behind the wall, which can increase soil pressure and lead to wall failure. Installing drainage solutions helps manage water flow and maintain wall stability.
What materials should be used for building a retaining wall?
It's important to use high-quality materials that are specifically designed for retaining walls, such as concrete blocks, natural stone, or treated timber, to ensure durability and longevity.
How can one ensure that the base of the retaining wall is level?
To ensure a level base, it's crucial to excavate the area carefully, use a level tool during the installation process, and regularly check for any irregularities throughout the building stages.